Share:
More Articles
Quote, Buy, Track!
We make it easy to get instant pricing and purchase your metal at the click of a button. Track your order progress, get notified when it ships, and follow your shipment online until it’s delivered. It’s that easy!
The PREN equations are derived from regression analysis (1). This correlates the chemical composition of a range of stainless grades with the results of pitting and crevice corrosion tests done in several aerated chloride solutions and chloride solutions containing other oxidizing species (2). As such, the relationship between PREN and the critical pitting temperature (CPT), as shown in Figure 1, is only applicable to these environments.
Figure 1 – Effect of PREN on the Critical Pitting Temperature in Ferric Chloride (ASTM G48C)
If creviced samples were tested, the critical crevice temperature (CCT) results would also have a linear relationship with PREN, but at lower temperatures.
Figure 2 shows examples of pitting and crevice corrosion.
Figure 2 – (a) Pitting Corrosion in a Forging (b) Crevice Corrosion of Threads of a Fastener
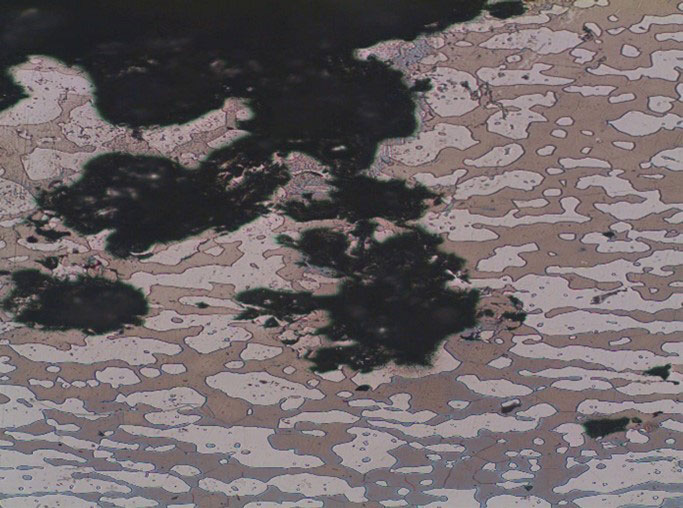
Figure A
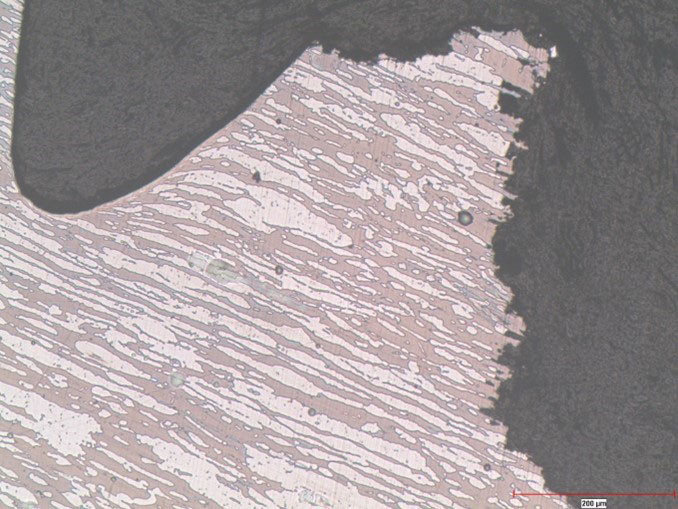
Figure B
The PREN equations are formulated based on the least squares linear fit between composition and the corrosion test result. The inclusion of the tungsten (W) factor “%W/2” is only done to improve the regression equation’s least squares fit. This is illustrated in Figure 1 for ZERON 100, where the arrow shows the effect of adding the “%W/2” term to the equation. The coefficients’ magnitude has no physical significance. Additionally, the nitrogen (N) content of an alloy is multiplied by 16 in the PREN equation. This does not mean nitrogen is 16 times more potent than chromium (Cr) in providing passivity. It is well known that an alloy must contain approximately 10.5% chromium to form a protective oxide film to be considered stainless.
The general applicability of the PREN equations relates only to alloys with a composition that falls within the range of compositions and steelmaking practice of the alloys tested. This is why some arguments are made about the magnitude of the coefficients used for stainless steels and why similar equations for nickel alloys include different elements and have very different coefficients (3).
The PREN equations commonly applied to stainless steels are:
– Equation 1 – Only applies to basic stainless steel grades.
o PREN = %Cr + 3.3 x %Mo
– Equation 2 – Applies to basic stainless steel grades and those deliberately alloyed with nitrogen.
o PREN = %Cr + 3.3 x %Mo + 16 x %N
– Equation 3 – Applies to basic stainless steel grades and those deliberately alloyed with nitrogen and tungsten.
o PREN = %Cr + 3.3 x (%Mo + %W/2) + 16 x %N
For alloys made when control of elements like sulfur (S) and manganese (Mn) in steel making was not as good as we have today, these elements were attributed negative coefficients (4). This is because of the formation of manganese sulfide inclusions that act as initiation sites for corrosion. Fortunately, modern steelmaking practice reduces the levels of sulfur and other minor elements to enhance corrosion resistance. However, in some new alloys, like lean duplex and austenitic stainless steels with high manganese contents, nickel levels have been reduced and substituted with manganese to lower costs. The conventional PREN relationship does not hold for these grades, and a negative coefficient is applied to the manganese (5,6).
– Equation 4 – Applies to lean duplex stainless steels.
o PREN = %Cr +3.3 x %Mo + 16 x (%N – Mn)
– Equation 5 – Applies to high Mn austenitic grades.
o PREN = %Cr + 3.3x %Mo +16 x (%N – %Mn/2)
However, chromium, molybdenum (Mo), and nitrogen levels should be considered only partially interchangeable. Minimum levels of each element must be present in a solid solution for the metallurgical synergies and the relationship between PREN and corrosion resistance to hold true (4). For example, a super austenitic grade with a PREN of 42.9 and 0.13% N performs worse than a super austenitic with a PREN of 42 with 0.2% N (7).
PREN levels have been correlated with CCT, measured in warm, natural seawater (8). Figure 3 shows that alloys with a CCT in ferric chloride at 35°C or higher correlate well with good resistance to crevice corrosion in warm seawater (i.e., zero sites attacked).
Figure 3 – Graph of the Results of Critical Crevice Temperature of a Range of Stainless Steels in Both Natural Seawater and Ferric Chloride Solution
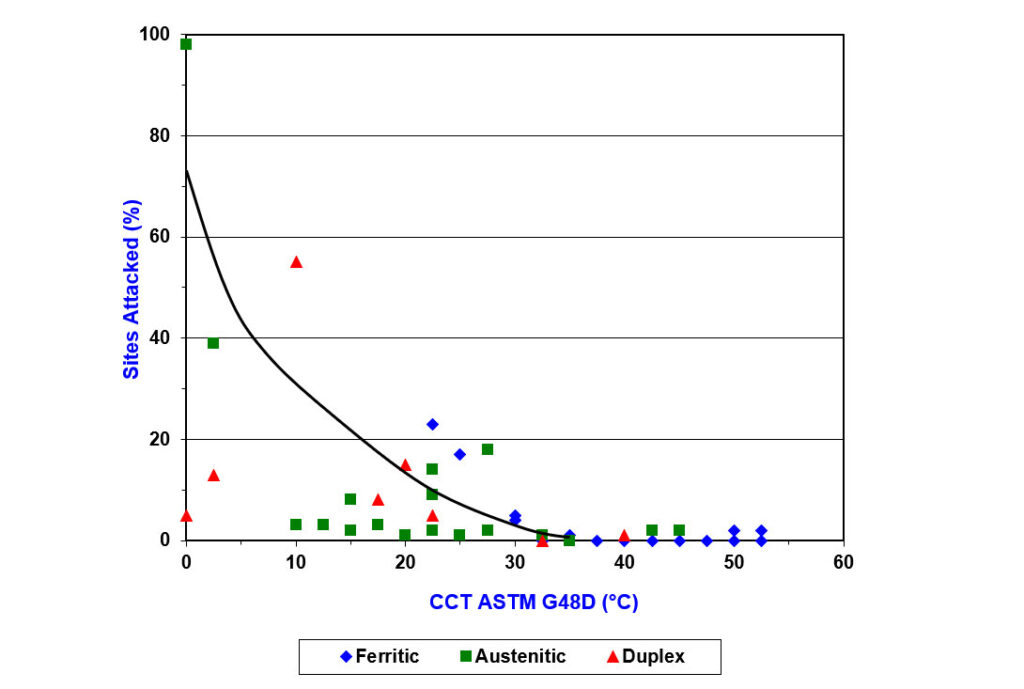
Figure 4 shows differences between ferritic, duplex, and austenitic grades when correlating CCT in a ferric chloride solution with PREN. When considering good CCT in seawater is provided by alloys with a CCT in ferric chloride solution of 35°C or higher, you can see that to achieve this, a minimum PREN of 35 is required for ferritic grades, 40 is needed for duplex grades, and 45 is needed for austenitic grades.
Figure 4 – Graph Showing How CCT in Ferric Chloride Solution Varies with PREN for a Range of Stainless Steels
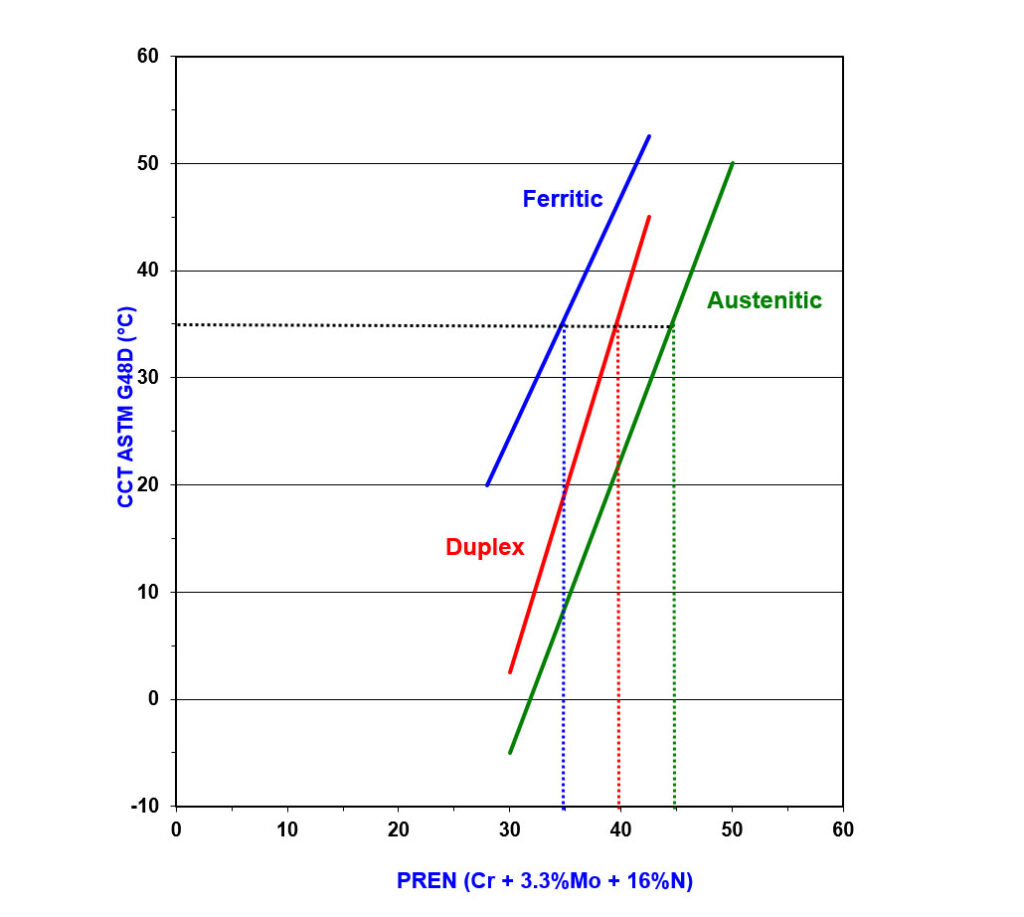
The relationship between PREN and corrosion resistance only holds if the alloys are properly manufactured. Heat treatment problems can cause phases to be formed that destroy corrosion resistance irrespective of the bulk composition (9). Equally, heat treatment at the wrong solution heat treatment temperature affects the partitioning of elements between the phases. This can cause a mismatch between the local PREN of the austenite and ferrite phases, which also causes the bulk PREN not to correlate so well with the corrosion resistance (10). Poor pickling can leave chromium-depleted surface layers that cause poor performance in stainless steels and nickel alloys (7,11).
Specifying PREN alone cannot be relied upon to achieve the expected level of corrosion resistance. For example, duplex alloys must be subject to cast and batch testing according to an appropriate material specification that includes corrosion, microstructure, and, for some grades, impact testing to check that the performance is as expected (12). The ferritiscope is a practical, non-destructive way of checking that individual parts don’t contain high levels of deleterious phases that destroy corrosion resistance (13,14).
The PREN number remains a highly convenient tool for establishing the relative corrosion resistance of different grades of stainless steel in oxidizing chloride environments. However, it constitutes a “point of entry” into the understanding and ranking of corrosion resistance of stainless grades. More detailed work is required to establish the suitability of stainless steels for a given application and to understand limits of use and potential susceptibility to other forms of corrosion like stress corrosion cracking.
References
1) K Lorenz, G. Medawar, Thyssenforschung 1, 3 (1969): p. 97-108.
2) J. E. Truman, UK Corrosion ’87, Brighton, England, October 1987, 26–28, 111.
3) B Craig “Clarifying the Applicability of PREN Equations: A Short-Focused Review”. Corrosion Journal.Org. April 2021, Vol 77. Issue 4. P382 to385.
4) KJ Blom and J Dagerbeck. Materials Performance. NACE, p 52 to 54. July 1983.
5) J. Charles, “Duplex Families and Applications: A Review, Part 2, “Stainless Steel World September (2015): p. 67-70
6) J. Charles, “Duplex Families and Applications: A Review, Part 3,“Stainless Steel World October (2015): p. 1-4.
7) EB Shone et al. “Stainless Steels as Replacement Materials for Copper Alloys in Seawater Handling Systems”. Trans. Inst. Marine Engineers, Vol.100, p193 to 199.
8) C Kovach and JD Redmond “Correlations between the CCT, PREn and Long-Term Crevice Corrosion Data for Stainless Steels” Proc. Conf. Corrosion ’93. NACE, Paper 267, New Orleans, USA, March 1993.
9) JO Nilsson and G Chi “The Physical Metallurgy of Duplex Stainless Steels” Proc. Conf. Duplex World 2010, Paper II.2, Beaune, France, October 13 to 15th, 2010.
10) L Garfias “Understanding Why PREN Alone Cannot be Used to Select Duplex Stainless Steels”. Proc. Conf. NACE. Dallas. Texas. USA. Paper 6005. March 2015.
11) JF Grubb et al “Surface chromium depletion and Corrosion Attack” Proc Conf NACE. Las Vegas, USA. Paper 04291, 2004
12) R Howard. et al. “Improving Manufacturing Quality of Duplex Stainless-Steel Components”. Proc. Conf. Duplex World 2010, Paper III.C.1, Beaune, France, October 13 to 15th, 2010.
13) Francis R. et al. Proc. Conf. Duplex World 2010, Paper III.C.4, Beaune, France, October 13 to 15th, 2010.
Buy Online Anytime
Our dashboard makes it even easier to shop online anytime from anywhere. Quote, buy, and track 24 hours a day.
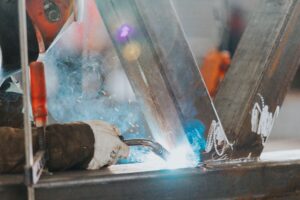
Welding Consumable Designations and Selection Criteria
Understanding welding consumable designations is essential for achieving strong, reliable welds. This guide breaks down AWS standards, electrode naming conventions, and key factors like polarity, base materials, and welding position to help you choose the right filler metal every time.
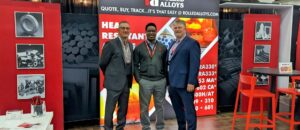
2025 Trade Shows
Come talk to a Rolled Alloys representative in person about your product needs! You can find us at these trade shows:
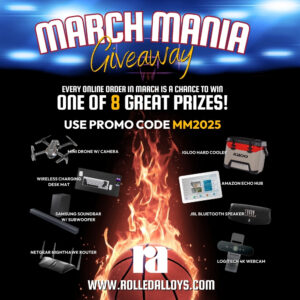
March Mania 2025
Every Online Order in March is a Chance to Win One of 8 Great Prizes!
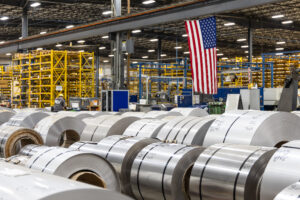
Instant Pricing on Nickel, Stainless Steel, Duplex, and Titanium
Get real-time pricing and availability for nickel, stainless steel, duplex, and titanium—all in one place.
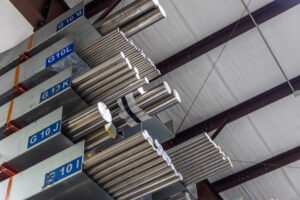
New and Expanded Stock for 2025
New Titanium, Stainless, Nickel and Cobalt in Stock Now – CP Ti Grade 2, 635, 718 and More!
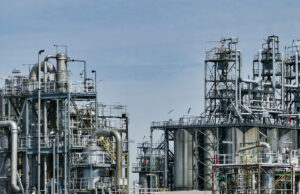
History and Uses of Alloy 800
Discover the evolution of Alloy 800, from its origins during the 1950s to modern derivatives like Alloy 800H/800HT. Learn about its high-temperature strength, petrochemical applications, and commercial availability today.