Share:
When molten metal (steel, stainless steel, or nickel alloys) solidifies, the center of an ingot or slab is the last to freeze.
While non-metallic impurities (oxides, nitrides, sulfides, silicides) settle throughout the ingot or slab, the greatest concentration of these inclusions settle along the solidification front. Consequently, the center of the product will have the greatest concentration of non-metallics. Voids, while extremely rare, can form small gas pockets during solidification, though they will likely heal during hot working.
When materials are extensively machined, an inclusion or cluster of inclusions can be seen on the final machined surface. These open inclusions can be detected by NDT or if the surface is fine enough, they can be seen with the naked eye. When this happens, the question is invariably, what is wrong with the material, and why weren’t they seen before? As stated previously, inclusions are naturally occurring. Before machining, inclusions contained within a material are sufficiently small, that they would not be detected by traditional NDT methods. After machining, it is not uncommon to see inclusions at the surface of a machined part or detect them through NDT. Oftentimes, these inclusions do not hamper the usability of material and are not sufficient causes for material rejection.
While inclusions are naturally occurring, they are more likely to be seen in titanium-stabilized materials, such as 321, since titanium nitrides tend to form large stringer inclusions.
Parts manufactured from precipitation-hardened materials, such as 17-4 stainless steel, frequently produce indications during magnetic particle inspections because the stringer inclusions can create magnetic fields, even if they are below the surface. Even though there is an indication, there are usually no voids present.
Most of the time, inclusions are harmless and non-detectable. Vacuum melting or consumable electrode remelting (VAR or ESR remelting) can be employed to reduce the size and frequency of inclusions. These processes can reduce the number of inclusions by an order of magnitude. However, there is a cost associated with these processes as well as minimum quantity requirements.
While it is prudent to use materials from higher-quality melt practices for aerospace and other critical applications where cleanliness is important, there are times when end users choose otherwise due to availability or cost. In such cases, end users must understand that inclusions can occasionally reveal themselves at the surface of the final part. These inclusions are often not a sufficient cause for material rejection, so the end user should bear the responsibility and cost. Occasionally, material may contain an irregularly high number of inclusions that hampers a material’s usability. In these circumstances, accommodations are often made.
Figure 1: Inclusions in a Nickel Alloy (Left), “Severe” Inclusions Highlighted by Magnetic Particle NDT (Right)
RA 253 MA Delivers High-Temp Performance in Industry Feature
RA 253 MA® Delivers High-Temp Performance in Industry Feature Back To All Articles Share: QUOTE, BUY, TRACK We make it easy to get instant pricing
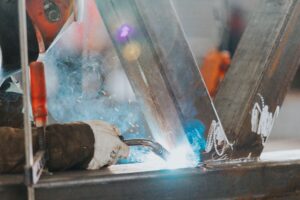
Welding Consumable Designations and Selection Criteria
Understanding welding consumable designations is essential for achieving strong, reliable welds. This guide breaks down AWS standards, electrode naming conventions, and key factors like polarity, base materials, and welding position to help you choose the right filler metal every time.
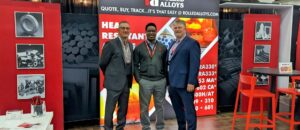
2025 Trade Shows
Come talk to a Rolled Alloys representative in person about your project. You can find us at these trade shows.
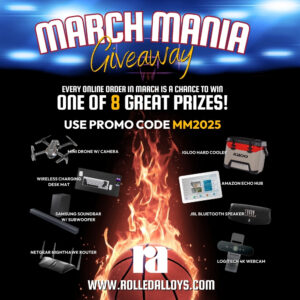
March Mania 2025
Every Online Order in March is a Chance to Win One of 8 Great Prizes!
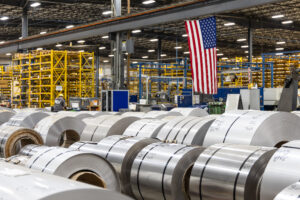
Instant Pricing on Nickel, Stainless Steel, Duplex, and Titanium
Get real-time pricing and availability for nickel, stainless steel, duplex, and titanium—all in one place.
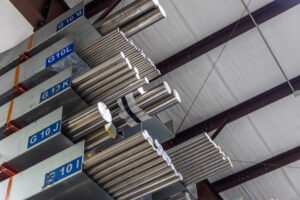
New and Expanded Stock for 2025
New Titanium, Stainless, Nickel and Cobalt in Stock Now – CP Ti Grade 2, 635, 718 and More!