Share:
Quote, Buy, Track!
We make it easy to get instant pricing and purchase your metal at the click of a button. Track your order progress, get notified when it ships, and follow your shipment online until it’s delivered. It’s that easy!
In most circumstances, machining stainless steel and nickel alloys is more difficult than machining low-alloy steels. However, there are a wide range of compositions, and some grades can have better machinability than mild steel.
The austenitic 300 series stainless steels, like 304/304L and 316/316L, are the most widely utilized stainless steel class. Their good corrosion resistance, formability, and weldability make them suitable for various applications. These characteristics are obtained by alloying nickel with chromium and iron. Adding nickel also results in alloys that work harden rapidly (strengthen through cold work). Therefore, while 300 series stainless steels are the most widely used, they are also the most difficult class of stainless to machine.
Recognizing the tendency for stainless and nickel alloys to cold work is the most important concept to remember when machining these grades. When a tool touches a workpiece to remove stock, it leaves behind a thin, work-hardened layer at the surface. Even though this layer is thin, overcoming the work-hardened layer on subsequent passes could prove to be difficult.
The five guiding principles below are the foundation for good stainless machining practices:
- Use a heavier feed than what you would typically utilize for mild steels. Heavier feeds are utilized to maintain the cut below the work-hardened surface. Dwelling on the surface or multiple thin cuts should be avoided.
- Taking a deeper cut will require more power. The equipment capability for stainless and nickel alloys is about 65% – 75% of that for mild steel. Use a slower speed than with mild steels. This will reduce heat and improve tool life.
- Since you are applying greater loads through the tool, the tools and fixtures must be as rigid as possible to avoid chatter and distortion. Minimize overhang or protrusion of both the tool and the workpiece.
- Keep tools sharp with recommended rake angles and clearances. Chip breakers may be beneficial for higher nickel-containing alloys.
- Proper cutting fluids are critical to maintain adequate lubrication and heat removal. The tool should be flooded with lubricant, which will help remove chips from the work area.
There are many variables in machining operations, so guidelines for speeds and feeds can be used as starting points. Guidelines for speeds and feeds for stainless steels, nickel alloys, and other specialty metals can be found on our website by clicking the below link:
Please contact the Rolled Alloys Metallurgical Services group at 1-800-521-0332 or submit your questions below.
Buy Online Anytime
Our dashboard makes it even easier to shop online anytime from anywhere. Quote, buy, and track 24 hours a day.
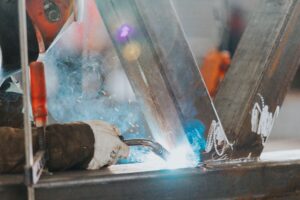
Welding Consumable Designations and Selection Criteria
Understanding welding consumable designations is essential for achieving strong, reliable welds. This guide breaks down AWS standards, electrode naming conventions, and key factors like polarity, base materials, and welding position to help you choose the right filler metal every time.
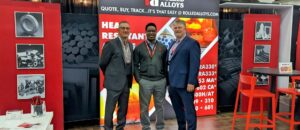
2025 Trade Shows
Come talk to a Rolled Alloys representative in person about your product needs! You can find us at these trade shows:
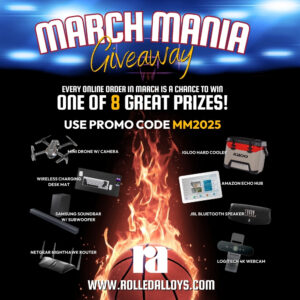
March Mania 2025
Every Online Order in March is a Chance to Win One of 8 Great Prizes!
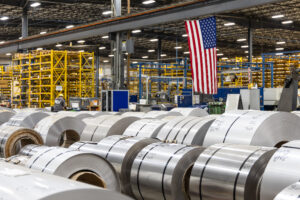
Instant Pricing on Nickel, Stainless Steel, Duplex, and Titanium
Get real-time pricing and availability for nickel, stainless steel, duplex, and titanium—all in one place.
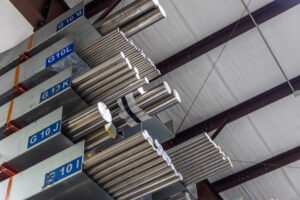
New and Expanded Stock for 2025
New Titanium, Stainless, Nickel and Cobalt in Stock Now – CP Ti Grade 2, 635, 718 and More!
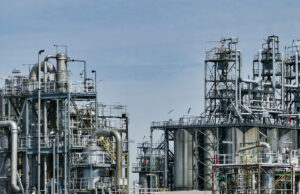
History and Uses of Alloy 800
Discover the evolution of Alloy 800, from its origins during the 1950s to modern derivatives like Alloy 800H/800HT. Learn about its high-temperature strength, petrochemical applications, and commercial availability today.