Share:
QUOTE, BUY, TRACK
We make it easy to get instant pricing and purchase your metal at the click of a button. Track your order progress, get notified when it ships, and follow your shipment online until it’s delivered. It’s that easy!
WATCH THE PRESENTATION BELOW
PRESENTATION SLIDES
Welcome, readers, to our exploration of best practices when utilizing duplex stainless steels. In today’s blog, we delve into the insights shared during a recent webinar conducted by Rolled Alloys, where Dr. Glenn Byrne, an esteemed expert in metallurgy, provided invaluable knowledge on this subject.
Meet your Speaker – Dr. Glenn Byrne
Dr. Glenn Byrne, the distinguished speaker of today’s webinar, brings a wealth of experience and expertise to the discussion on best practices for utilizing duplex stainless steel. With a background in metallurgy from the prestigious University of Sheffield, Dr. Byrne has dedicated his career to exploring the intricate relationship between manufacturing methods, microstructure properties, and the applications of various steels.
His professional journey has seen him contribute significantly to the field, from his tenure at the Corrosion and Protection Center for Industrial Services to his pivotal role at Weir Materials and Foundries. Dr. Byrne’s passion lies in understanding the mechanisms of steel behavior and dissecting the root causes of failures to pave the way for continuous improvement.
Today’s webinar is a testament to Dr. Byrne’s dedication to knowledge dissemination and his unwavering pursuit of excellence in metallurgical practices. We thank Dr. Byrne for sharing his expertise and leading this enlightening discussion.
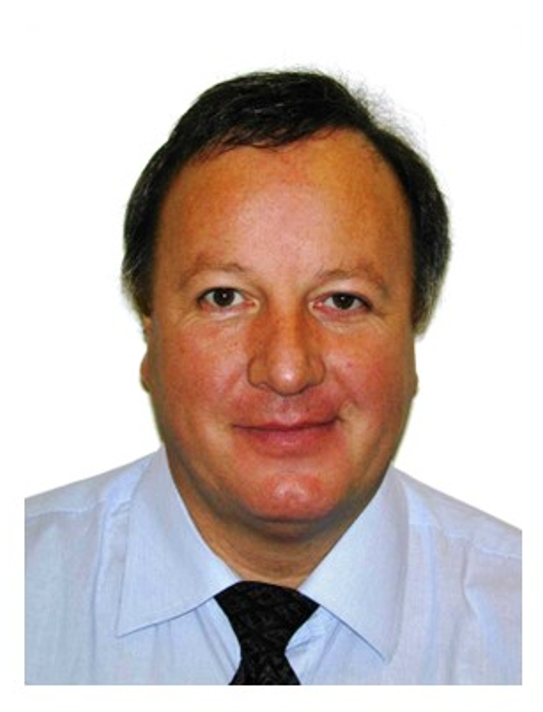
Understanding Duplex Stainless Steel
Duplex stainless steel is a fascinating material composed of two phases: ferrite and austenite. These phases contribute unique properties to the steel. Ferrite offers strength but can be brittle, while austenite provides toughness. We achieve optimal strength, toughness, and corrosion resistance by maintaining a balanced proportion of each phase.
However, if not careful, manufacturing processes can introduce deleterious third phases, such as the sigma phase, into the microstructure. Sigma phase particles can significantly compromise corrosion resistance and toughness, leading to application failures. Detecting these deleterious phases requires meticulous testing, including microstructure examinations and corrosion tests.
Metallurgical Quality and Base Materials
Dr. Byrne emphasized the critical importance of ensuring metallurgical quality in base materials. Sophisticated users go beyond ASTM standards, implementing supplementary testing to confirm freedom from harmful phases. Techniques like in-situ metallography can be used to test components that have already been placed into service where lab testing is impractical or as a rough quality check.
Welding Considerations
Welding introduces its own set of challenges, particularly regarding nitrogen loss and sigma phase formation. Dr. Byrne discussed the significance of controlling heat input during welding to prevent nitrogen loss and minimize the risk of sigma phase formation. Weld procedure qualification becomes crucial, requiring thorough testing to ensure weld integrity and performance.
Recommendations for Success
Throughout the webinar, Dr. Byrne provided several recommendations for achieving success with duplex stainless steel:
1. Partner with experienced suppliers capable of delivering high-quality materials.
2. Implement rigorous testing protocols, including microstructure, corrosion, and impact tests.
3. Optimize welding practices to minimize heat input and control the formation of deleterious phases.
Conclusion
In conclusion, utilizing duplex stainless steel effectively requires a deep understanding of metallurgical principles and meticulous attention to manufacturing and welding processes. By following best practices outlined by experts like Dr. Byrne and leveraging testing techniques, manufacturers can ensure the integrity and reliability of their products in demanding applications.
Thank you for joining us on this journey through the world of duplex stainless steel. We hope this blog and webinar provide valuable insights into maximizing the performance of these remarkable materials. Stay tuned for more informative content from Rolled Alloys as we continue to explore the frontiers of metallurgy and materials science.
Please contact the Rolled Alloys metallurgical Services group at 1-800-521-0332 or submit your questions below.
RA 253 MA Delivers High-Temp Performance in Industry Feature
RA 253 MA® Delivers High-Temp Performance in Industry Feature Back To All Articles Share: QUOTE, BUY, TRACK We make it easy to get instant pricing
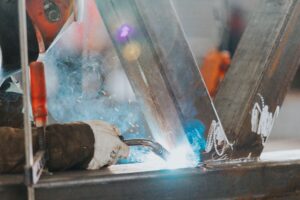
Welding Consumable Designations and Selection Criteria
Understanding welding consumable designations is essential for achieving strong, reliable welds. This guide breaks down AWS standards, electrode naming conventions, and key factors like polarity, base materials, and welding position to help you choose the right filler metal every time.
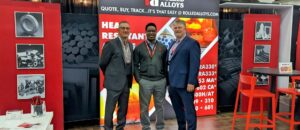
2025 Trade Shows
Come talk to a Rolled Alloys representative in person about your project. You can find us at these trade shows.
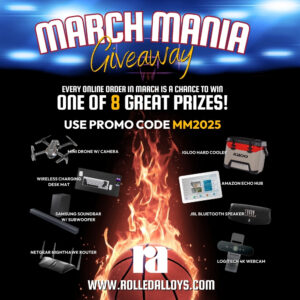
March Mania 2025
Every Online Order in March is a Chance to Win One of 8 Great Prizes!
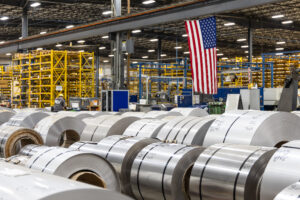
Instant Pricing on Nickel, Stainless Steel, Duplex, and Titanium
Get real-time pricing and availability for nickel, stainless steel, duplex, and titanium—all in one place.
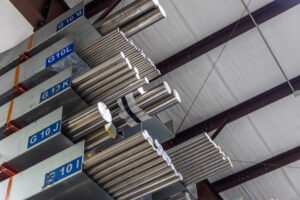
New and Expanded Stock for 2025
New Titanium, Stainless, Nickel and Cobalt in Stock Now – CP Ti Grade 2, 635, 718 and More!